Automated PU Roller Inspection Solution
Pain Points Solution Advantages
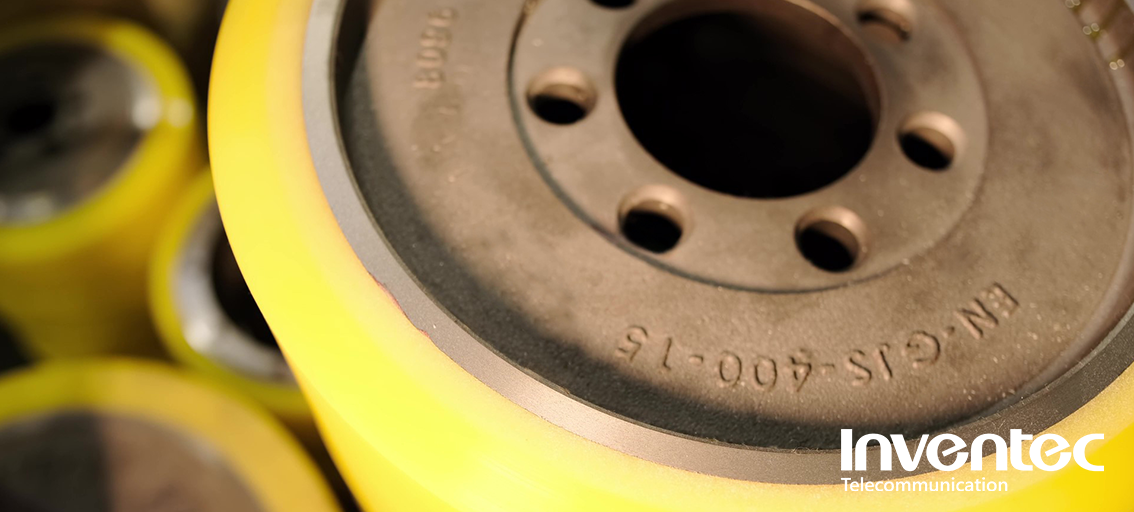
PU friction rollers are essential tools for processing high-quality fibers, particularly during the false twisting process (a technique that alters fiber structure during spinning). During this process, the rollers must remain free of impurities to ensure stable yarn quality. Traditional PU friction wheel inspection relies on manual labor, resulting in high costs, low efficiency, and lengthy training periods, which impact production line stability. Inventec’s automated PU roller inspection solution accurately detects defects such as bubbles, black spots, and bonding issues, achieving a 90% detection rate to significantly enhance quality. Its intelligent interface lowers the technical threshold, shortens training time, and reduces reliance on manual labor. Additionally, the modular inspection station offers flexible deployment and seamless integration with downstream processes, helping businesses cut labor costs, optimize production management, and create a highly efficient automated manufacturing environment!
Pain Points for Plastic Manufacturing Industry
- Manual inspection of PU friction rollers is labor-intensive and costly.
Traditional industries face significant challenges in recruiting workers due to declining birth rates and changes in population demographics. Many young individuals prefer urban employment, making it increasingly difficult for traditional industries to secure a stable workforce. This reliance on manual inspection not only results in high labor costs but also introduces uncertainty in workforce availability. As a result, there is a pressing need for automated inspection technology to reduce dependence on manual labor, lower costs, and enhance production line efficiency and stability.
- Inspection requires extensive training and it is inefficient.
Historically, the inspection of PU friction rollers has relied heavily on skilled, experienced workers with excellent vision and attention to detail. These workers act almost like "human scanners," capable of detecting even the smallest defects. However, developing such expertise often takes months or even years of training. When experienced employees leave, companies must train new workers from scratch, leading to inefficiencies and potential production delays. Additionally, as workers' vision and focus naturally decline over time, error rates and inspection inconsistencies increase, further impacting quality.
Solutions
- AI Automated Inspection System
This product is specifically designed for inspecting PU friction rollers, capable of accurately identifying defects such as bubbles, black spots, filament residue, inner wheel issues, and poor adhesion. It supports various PU roller colors, achieving a defect detection accuracy of up to 90%, significantly improving product quality.
- Smart Operation
With an intuitive user interface, employees only need to perform re-inspection tasks. Even non-specialized personnel can quickly adapt, reducing operational complexity, significantly shortening training time, and minimizing workforce requirements for shift rotations. This optimization enhances overall resource allocation.
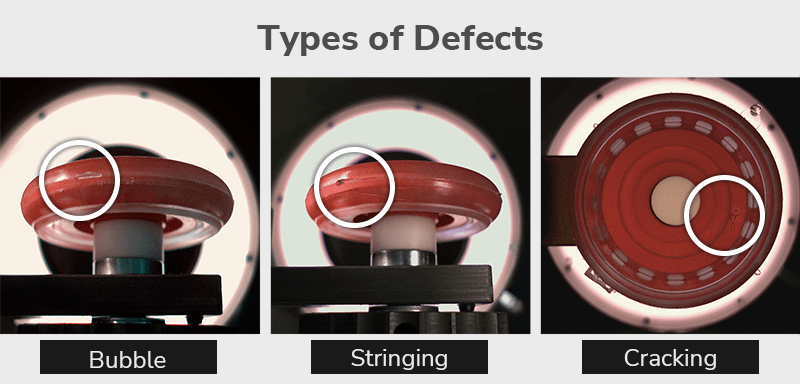
Solution Advantages
- Modular Expansion of AI Inspection Stations
Inventec’s modular inspection system features a flexible, plug-and-play design that adapts to various production environments without requiring major modifications to existing lines. This solution enables the rapid integration of AI-AOI smart inspection technology, allowing manufacturers to easily expand their inspection coverage across different machine types and production settings. With its easy deployment and scalability, businesses can seamlessly implement high-efficiency defect detection to enhance quality control.
- Seamless Integration with Manufacturer Processes
The modular inspection stations seamlessly integrate with downstream processes such as laser engraving, automated packaging, and other production steps, fully catering to customer-specific requirements within their facilities.
- Reduction in Labor Costs and Enhanced Workforce Efficiency
Automated inspection systems drastically reduce reliance on manual labor, addressing recruitment and retention challenges while decreasing the need for three-shift staffing and temporary workforce adjustments. Companies save on the time and costs associated with long-term training of skilled workers and eliminate issues caused by employee turnover. The system's high efficiency enables businesses to reallocate resources to more strategic activities, thereby boosting competitiveness across the board.
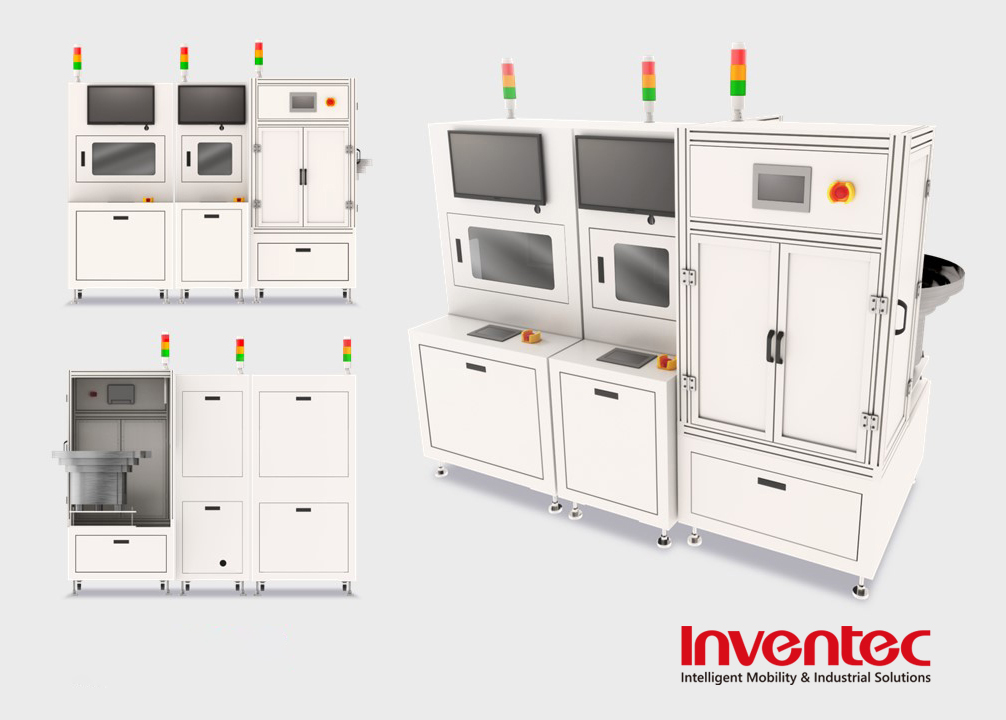
|