Efficient High-Value Fabric Inspection Solution
Pain Points Solution Advantages
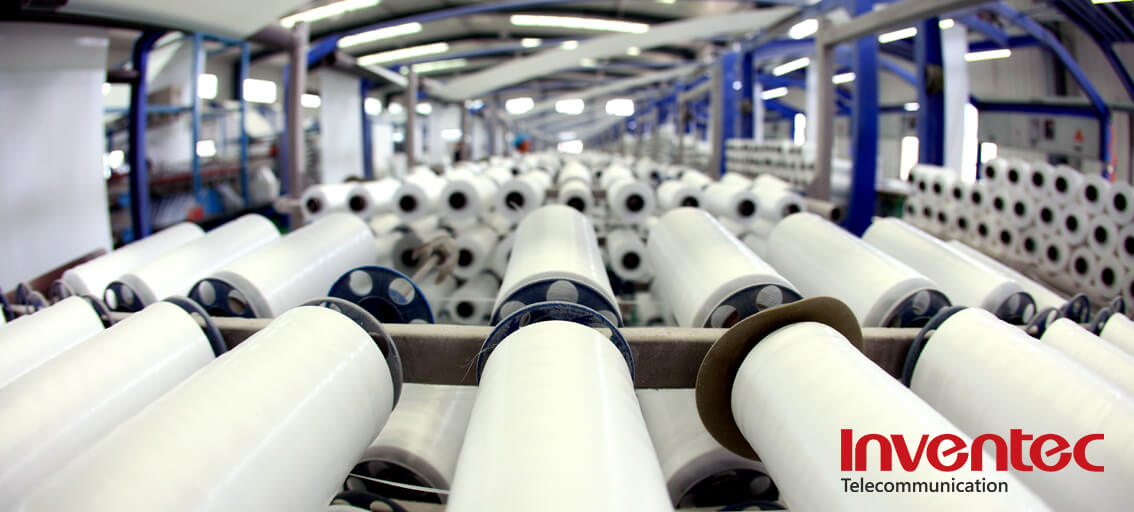 For large textile and plastic factories, low manual inspection efficiency often leads to missed minor defects, resulting in high scrap costs and management challenges. Inventec’s high-efficiency defect detection solution offers flexible deployment, quickly adapts to various production environments, accurately identifies fabric defects, and provides real-time alerts to minimize waste. Additionally, the system automatically records defect data, enhancing tracking and management efficiency, transforming inspectors from defect seekers into quality managers. By reducing labor burdens and improving production efficiency, it paves the way for a new era of smart and efficient quality control.
Pain Points for Plastic Textile Industry
- Manual inspection is inefficient and fails to identify defects in real time.
In large production facilities spanning over 10,000 square meters, manual inspection struggles to meet efficiency demands. Inspectors must frequently shuttle between hundreds of weaving machines to identify fabric defects. However, limited staffing and prolonged inspection intervals often result in minor defects being overlooked or discovered too late, leading to entire batches being scrapped.
- Inspection records rely on manual input, resulting in scattered management and difficulty tracking defect issues.
Traditional weaving machines cannot automatically generate inspection reports or error logs, forcing factories to rely on manual recording of defect issues. This approach carries risks of incomplete, inaccurate, or missing records. When tracing the root cause of problems in specific product batches, significant time is often spent searching through handwritten notes or multiple spreadsheets, drastically reducing tracking efficiency. Furthermore, inspectors working in environments with hundreds of weaving machines endure noise levels exceeding 100 decibels for extended periods, leading to fatigue and reduced attentiveness.
Solutions
- Flexible Deployment of Mobile Inspection Machines
Traditional fixed inspection equipment often requires disassembly and structural modifications to the facility, increasing deployment time and costs while disrupting production lines. Our mobile inspection machines, designed with modularity in mind, eliminate the need for fixed installation and can be deployed flexibly across multiple production areas. This approach allows for rapid inspections and accommodates various weaving machine models and facility layouts, mitigating risks associated with facility modifications or production downtime. The mobile inspection machines are equipped with real-time defect notification capabilities, accurately detecting various fabric defects during production. Inspectors can act on system alerts to quickly halt machines and address defective products, preventing further waste and significantly reducing scrap costs while enhancing production efficiency.
- Systematic Recording of Defect Inspection Processes
Our inspection system not only accurately handles diverse fabric defects such as broken yarns, stains, fuzz, and skipped threads but also automates the recording and categorization of inspection data. This provides efficient data support for production management. Through detailed defect record reports, managers can easily trace the root cause of issues, quickly identify problematic batches, and optimize production processes for specific problems. Additionally, the systemized data facilitates defect trend analysis and identification of frequent issues, helping companies proactively prevent potential problems and achieve continuous process improvement.
Solution Advantages
- Effective and Integrated Defect Detection Solutions
Traditional defect detection devices typically require fixed installation of cameras and mounts, necessitating production downtime for setup. This not only increases construction costs but also disrupts production efficiency. Our mobile inspection stations offer high flexibility, allowing rapid deployment in areas requiring inspection without halting production. This seamless integration eliminates the interference of traditional detection solutions with production capacity.
- Reduction in Labor Costs and Enhancement of Workforce Skills
Automated defect detection solutions significantly reduce reliance on manual inspection, minimizing quality issues caused by staff shortages, fatigue, or human error. The high-accuracy detection and real-time alerting features enable inspectors to focus on defect verification and issue resolution, transforming their role from "defect finders" to "quality managers." This shift greatly enhances the added value and professional capabilities of personnel. Additionally, the systematic recording and tracking functions reduce the burden of manual record-keeping, providing clear problem analysis and reports for management, further supporting decision-making optimization and continuous improvement. This creates an efficient and professional production environment for enterprises.
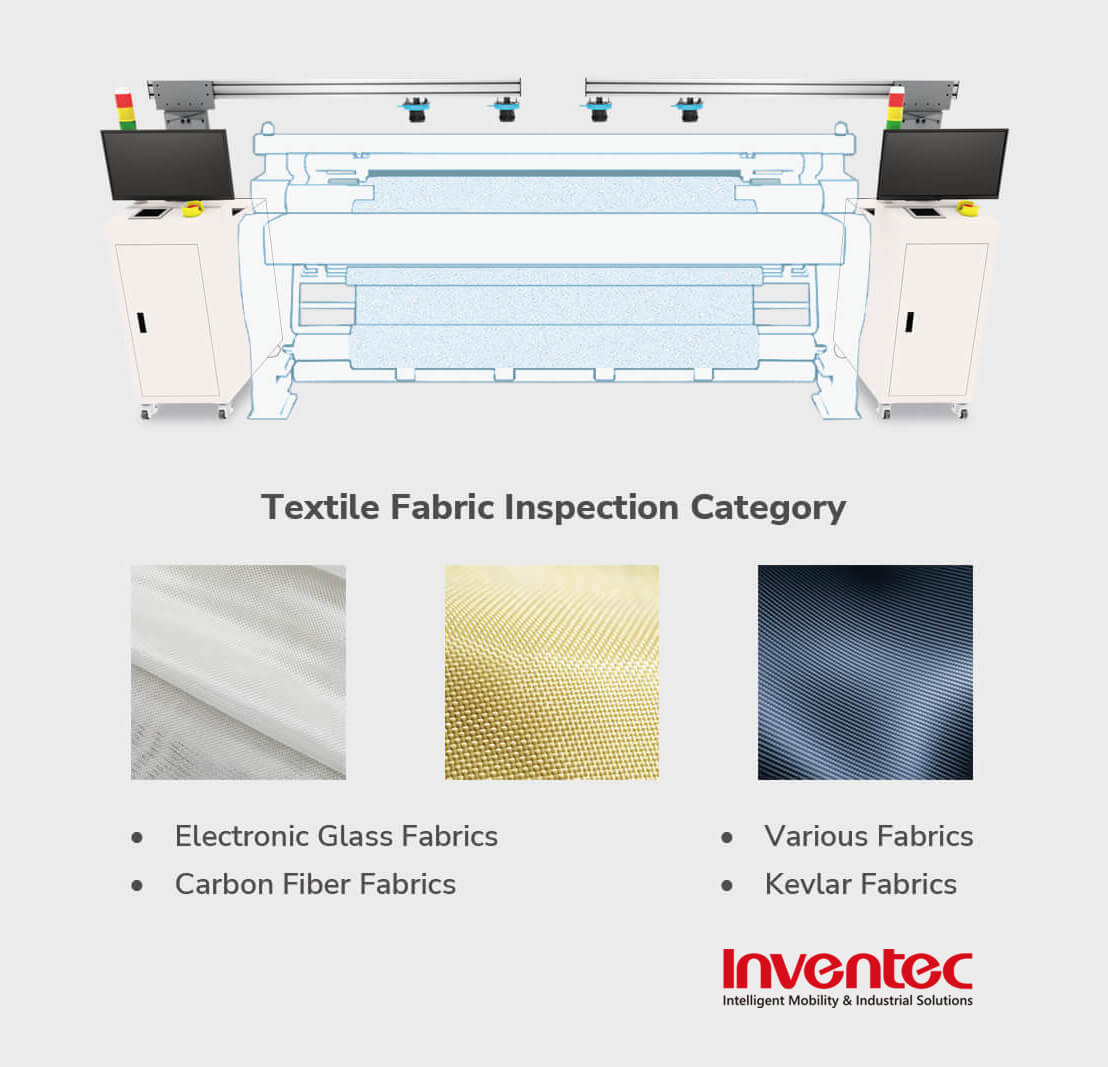
|